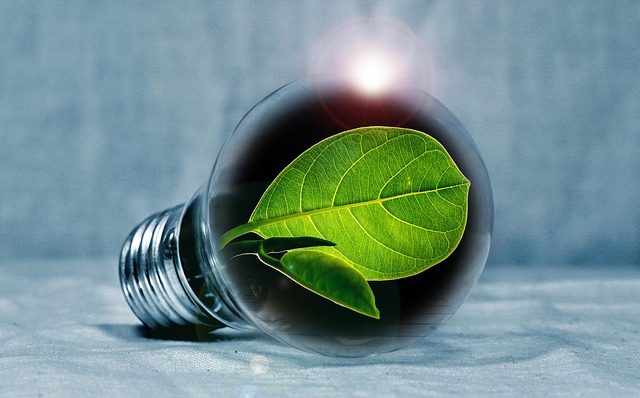
Hollow Oscillating Disk Pumps and Energy Efficiency
What You Need to Know:
In today’s industrial landscape, energy efficiency is not only crucial for reducing operational costs but also for minimizing environmental impact. Volumetric hollow oscillating disk pumps play a key role in a variety of industries, from petrochemical to food processing, fron pharmaceutical to agriculture. Understanding how to optimize the energy efficiency of these pumps is essential to improving industrial process performance and promoting sustainable use of energy resources. This article delves into the features of volumetric hollow oscillating disk pumps and the challenges related to energy efficiency.
Introduction to Volumetric Hollow Oscillating Disk Pumps:
Volumetric hollow oscillating disk pumps are mechanical components designed to handle fluids by directly displacing a fixed volume of fluid from the suction side to the discharge side. Unlike centrifugal pumps, which rely on velocity to generate flow, volumetric pumps ensure a constant flow regardless of system pressure, making them ideal for applications requiring precision and control.
Energy Efficiency Challenges in Pumps
Key challenges in achieving energy efficiency include:
- Internal Leakage: Tolerances between hydraulic parts can lead to internal fluid leakage, reducing volumetric efficiency and increasing energy consumption.
- Mechanical Friction: Interaction between moving parts generates friction, dissipating energy as heat.
- Improper Sizing: An oversized pump operating outside its peak efficiency range leads to energy waste.
- Insufficient Maintenance: Component wear and lack of regular maintenance can undermine pump performance and increase energy use.
Strategies to Enhance Energy Efficiency:
To address these challenges, M Pompe has developed various strategies and technological solutions aimed to optimize energy efficiency.
Design and Material Optimization:
The adoption of advanced materials and design improvements have significantly reduced internal losses and mechanical friction.
The use of high-strength metal alloys and composite materials minimizes component wear, while innovative surface coatings reduce friction between moving parts.
Optimizing tolerances between components minimizes internal fluid losses, improving volumetric efficiency.
Collaboration between the technical department and the R&D team has resulted in pumps with enhanced reliability and safety, reducing power consumption to a minimum.
Speed Control with Inverters:
Integrating inverters or variable frequency drives (VFDs) into pumping systems enables speed regulation based on actual demand. This approach adjusts pump operation to process requirements, avoiding full-capacity operation when unnecessary and reducing energy consumption.
Regular and Scheduled Maintenance:
Preventive maintenance is crucial for maintaining pump energy efficiency. Regular inspections and replacement of worn components prevent performance reduction and ensure that the pump operates near its optimal efficiency point. Training technical staff in best maintenance practices extends equipment lifespan and reduces overall operational costs.
Proper Pump Sizing:
Accurate system analysis is essential for selecting a pump with suitable characteristics. Proper sizing ensures the pump operates within its optimal efficiency range, avoiding energy waste associated with oversized or undersized pumps.
High-Efficiency Electric Motors:
Using IE3-class or higher electric motors helps reduce energy consumption. These motors are designed to deliver superior efficiency compared to standard models, resulting in significant long-term energy savings.
Advanced Sealing Technologies:
Fluid losses through seals can be a source of energy inefficiency. Advanced sealing technologies, such as double cartridge mechanical seals or magnetic drive systems (MAG Series), eliminate fluid leaks, enhancing overall pump efficiency.
Practical Applications and Economic Benefits:
Adopting these strategies and innovative technologies offers numerous advantages for businesses:
- Energy Cost Reduction: Improved energy efficiency directly translates to lower energy bills, reducing overall operating costs.
- Increased Productivity: More efficient pumps ensure a constant and reliable flow, improving production quality and minimizing downtime.
- Environmental Sustainability: Reduced energy consumption leads to lower greenhouse gas emissions, contributing to environmental sustainability goals.
Final Remarks:
Energy efficiency in pumps is a fundamental aspect requiring an integrated approach, combining advanced technological solutions with optimal operational practices. Companies should view investment in innovative technologies not as a cost but as an opportunity to enhance their products and contribute to a more sustainable future. M Pompe is at the forefront of this field, introducing cutting-edge products that deliver both technical excellence and energy efficiency.